
FDA-Registered Pharmaceutical Manufacturer with
Third-Party Laboratory Testing

In the context of product safety, quality assurance, and consumer trust, providing specific certificates related to purity is crucial. These documents serve various purposes that benefit both consumers and manufacturers. Below is a detailed explanation of each certificate’s importance.
The following information covers our company's administrative structure, quality control policies, manufacturing operations, laboratory testing procedures, and adherence to approved current good manufacturing practices throughout our operations. Additionally, we confirm that the company from which we source our lipotropic ingredients is based in the United States and is FDA registered.

Our On-Going Commitment to Transparency and Quality
At Black Label Lipo, we prioritize sourcing, vetting, and manufacturing practices that meet the highest standards. While many people may not realize the lengths we go to ensure the exceptional quality of our products, transparency is at the core of our mission. It’s important to note that lipotropics are not classified as prescription products—they are regulated as supplements. This distinction exists because lobbyists have actively worked to keep lipotropics accessible to individuals who might not have access to healthcare or the financial means to obtain prescription-based alternatives.
Why We Chose Not to Use Compounding Pharmacies
Our decision to avoid compounding pharmacies is not due to a lack of trust in their services, but rather because they are unable to meet the extensive ingredient requirements of our proprietary formula. Compounding pharmacies typically work with 3–5 ingredients, which does not align with the advanced, multi-faceted nature of our lipotropic blend. It’s also important to clarify a common misconception about compounding pharmacies. While FDA-regulated compounding pharmacies may create a lipotropic or hypertropic formula, this does not mean that the resulting product is FDA-approved. Compounded products are custom formulations made to meet specific patient needs, but they do not go through the rigorous FDA approval process required for commercial drugs. The FDA approval process involves extensive testing for safety, efficacy, and quality, which compounded products are not subject to. Instead, compounded formulations fall under the oversight of state pharmacy boards and must comply with FDA regulations for compounding practices. However, the absence of FDA approval means there is no guarantee of the product's clinical effectiveness or long-term safety.
At Black Label Lipo, we take an entirely different approach. Rather than relying on compounding pharmacies, we develop our formulas using advanced FDA approved manufacturing processes and thoroughly vetted non-GMO, organic, and vegan ingredients. This ensures that every product we offer meets stringent quality standards, offering a level of consistency and reliability that compounded products cannot match.
No Compromise on Quality
At Black Label Lipo, we refuse to compromise on quality or effectiveness. We deliberately avoid creating a standard lipotropic blend because we understand that many individuals need a more advanced, holistic solution. Unlike traditional lipotropics, which often offer limited benefits, our formula is designed to address the unique health challenges faced by people who have struggled with weight loss for years.
These challenges may include, but are not limited to:
- Diabetes
- Sleep apnea
- Hypertension
- High cholesterol
- Fatty liver disease
- Vitamin imbalances
- Elevated cortisol levels
- Other health obstacles
Our proprietary formula takes a comprehensive approach, balancing the entire body to address these underlying issues. By doing so, we help individuals achieve lasting results, far beyond what standard lipotropics or compounded formulas can provide. This is why so many of our customers have experienced life-changing transformations using our products.
Certifications for Quality and Safety
To further demonstrate our commitment to transparency and quality, we are releasing the following certifications to the public:
1. Certificate of Analysis (COA) - Confirms the composition, purity, and potency of our formulas.
2. Material Safety Data Sheet (MSDS) - Provides safety guidelines and precautions for handling our products.
3. Vegan Statement - Certifies that our products are free from animal-derived ingredients and were not tested on animals.
4. Allergen Statement - Identifies potential allergens or cross-contamination risks.
5. Nutritional Statement - Details the nutritional content of our formulas, including macronutrients and micronutrients.
6. BSE/TSE Certification - Ensures our products are free from materials derived from animals impacted by BSE/TSE diseases. These certifications cover every ingredient in our Lipotropic C formula, including all 9 fat burners, 8 soluble B vitamins, and the vitamins and trace minerals used in our injectable products. This sets a new standard for transparency and quality assurance in the industry.
Why This Matters
By refusing to compromise on ingredient and manufacturing standards, Black Label Lipo delivers products that address the root causes of weight loss challenges. Our commitment to transparency through certifications ensures that customers can trust the safety, effectiveness, and ethical sourcing of our products. While compounding pharmacies may create custom lipotropic or hypertropic formulas, the absence of FDA approval for those products means they cannot guarantee the same level of efficacy and long-term safety. Black Label Lipo’s proprietary formulas, on the other hand, are created with a focus on science-backed ingredients, holistic solutions, and measurable results. This approach is why Black Label Lipo stands apart in the industry and why so many individuals have achieved unprecedented results with our formulas. We’re proud to take this step forward in setting a new standard for quality and accountability.
Third Pary Manufacturing Compliance
Is the company ISO registered? No
Is the company registered by the FDA? Yes
Registration number: -------3434
Date of last FDA inspection (if any): January 8, 2020
Did you receive a notice of observation/citation (e.g. FDA-483)? No
How does the supplier comply with applicable elements of cGMP guidelines?
Has developed a comprehensive list of company and industry-specific cGMP Standard
Operating Procedures (SOP) as required by the FDA. All employees are trained to follow the SOPs
and instructed in all applicable cGMP requirements in every facet of company operations. Revisions
are made as required by SOPs and an ongoing employee cGMP training program is conducted.
Corporate bioterrorism act compliance? Registered
Have you had a recall in the last 2 years? No
Is there an organizational chart? Yes
Is there a Quality Control program in place? Yes
Does a quality manual exist and is it supported by top management? Yes
Are management review meetings held? Yes
Are quality procedures in place and available to all employees affecting quality? Yes
Third Party Quality Control
Do you have a Quality Control Unit? Yes
Is your facility audited at least annually by an accredited cGMP organization? Which One? No
Is there a documented process for supplier survey and evaluation? Yes
Are suppliers evaluated to assure that material supplied meets requirements? Yes
Is the approved supplier list available to all employees? The approved supplier list is available to all
employees who require access.
Are incoming materials inspected for conformity to specifications? Yes. All incoming material is
placed in HOLD in the warehouse until COA’s, laboratory testing and physical assessment confirms
conformity to specifications.
If purchased material is rejected, is it segregated and returned to the supplier? Yes. Rejected
material is placed into the QUARANTINE area of the warehouse until it is returned to the supplier.
Are receiving inspections documented? Yes. Receiving logs are filled out as shipments arrive. The
receiving checklist includes inspecting all carriers for cleanliness, inspecting all shipments for any
damages or contamination and certifying that all incoming materials are free of pests.
Do Quality Control personnel have the authority to stop nonconforming materials from being
released for use or shipped to customers? Yes. No material is released for use or shipped to customers without Quality Unit approval.
Is there a written procedure for identification and traceability for all materials in place? Yes. All
material processed at has both the original supplier's name and batch number and an assigned lot number listed in manufacturing batch records for immediate traceability.
Is QA/QC responsible for review of all production records and release of finished products? Yes.
All master manufacturing records, manufacturing batch records and any related production records are
reviewed by the Quality Unit at several in-process checkpoints and kept on file for future use. All
products are physically inspected by Quality Unit personnel at several in-process checkpoints and the
finished product undergoes a final inspection prior to release to customers.
Do you have a Document Control/Change Control program in place? Yes. All documents are under
the control of the Quality Unit and regularly updated, reviewed and filed as needed. Changes to any
procedures or processes are documented under the provisions of the PureBulk SOPs governing
production deviations and document control/change control.
Are adequate controls in effect to prevent use of obsolete documents and specifications? Yes. All
obsolete or outdated documents and specifications are securely archived. Only one current working
version of each document is available to employees at any given time.
Is there a documented internal audit program in place? Yes.
Third Party Manufacturing
Please provide the number of different products manufactured in this same building?
270 raw materials at this location.
Do you have a validated system in place for products purchased by customers? Yes. Identity
and purity of all materials are validated prior to sale and shipment. Records of all customer
purchases are kept on file.
Do you have a GMP training program in place? Yes. All current and new employees are trained incGMP policies, with refresher courses and training updates required annually.
Do you have a recall program in place? Yes. A recall SOP details responsibilities and procedures to
be followed in the event of a recall. Mock recalls are performed at least annually.
Do you have a cleaning and disinfecting program for the production facility and equipment in
place? Yes. SOPs for cleaning, disinfecting and maintenance of all areas of the facility and
equipment are in place. Employees are regularly trained in the procedures. Daily logs documenting
completed cleaning are kept and filed.
Do you have a calibration program in place? Yes.
Do you have a maintenance program in place? Yes.
Do you have a line-clearance program in place? Yes.
Do you have an environmental monitoring program in place? Yes.
Do you have a pest control program in place? Yes.
Do you have a record retention program in place? Yes.
Third Party Testing Laboratories
What type of testing/study do you do at this site – analytical, microbial, and animal? There is no
testing done on-site. Documented third-party testing (assay, heavy metal (if applicable), microbial)
by qualified contract laboratories are used to meet FDA testing requirements to ensure potency
and purity standards are met.
Do you have a QA unit? Yes.
Do you use validated test methods for analysis? Yes.
Do you use validated equipment? Yes. Note: NIST-traceable scales that are certified by the state of
Oregon are used in all facets of production.
How long do you maintain records? 3 years

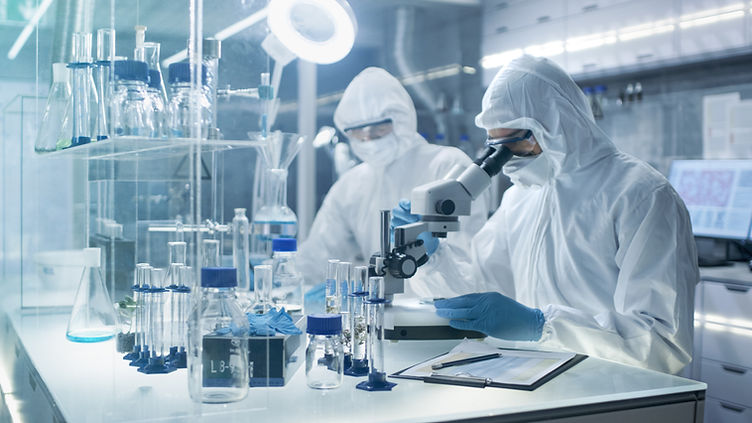